Gaskets
Gail (@GailNM) was kind enough to cut gaskets for me on my last engine. This time around I decided to develop the capability myself. It is something I want to be able to do going forward.
My first task was to procure PTFE film in .005″, .010″ and .020″ thicknesses. Fortunately, a plastic supply house is located within reasonable driving distance. Unfortunately, they do not like to deal with the little guy. I wanted a couple of square feet of each. They brought out the quote- 25$ per thickness, $75 total. They wanted to charge me a minimum of 1 pound of each size at $25 a pound. Who ever heard of such a thing, who buys rolls of PTFE film by the pound? Well I found another outfit that sold the film by the foot at pretty reasonable prices, but the shipping was $20. I bit the bullet and spent a total of $55 for the PTFE film I needed and have enough for several engines.
My second task was to obtain a cutter, after some research I settled on this from amazon:
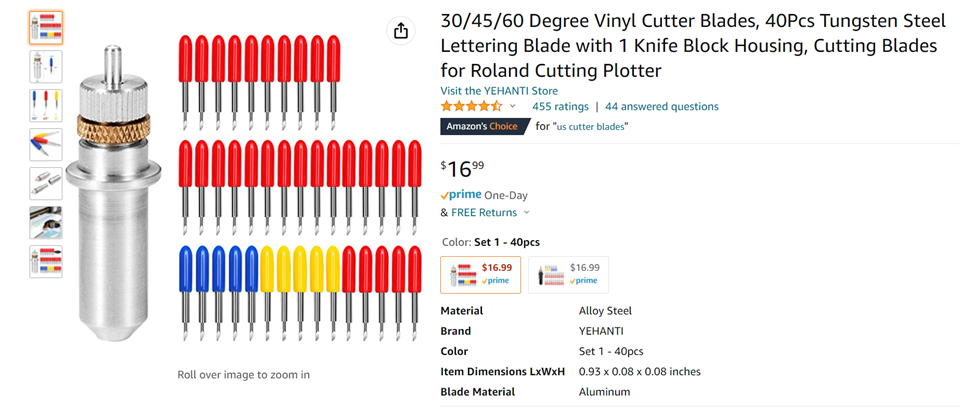
It works very well. I decided to use the 3E printer to do the cutting. The reason I decided to go this route was that the 3D printer has an auto bed leveling feature. The cutter needs to be held at a very consistent distance over the material being cut.
I used Fusion 360 to create the tool path. I could not make Fusion 360 create a Gcode file the 3D printer was happy with, the formats were too different and I could not find a post processor to do what I wanted. So I wrote a Python script to convert from “milling” Gcode to “3D printer” Gcode. This of course took some trial and error to get right.
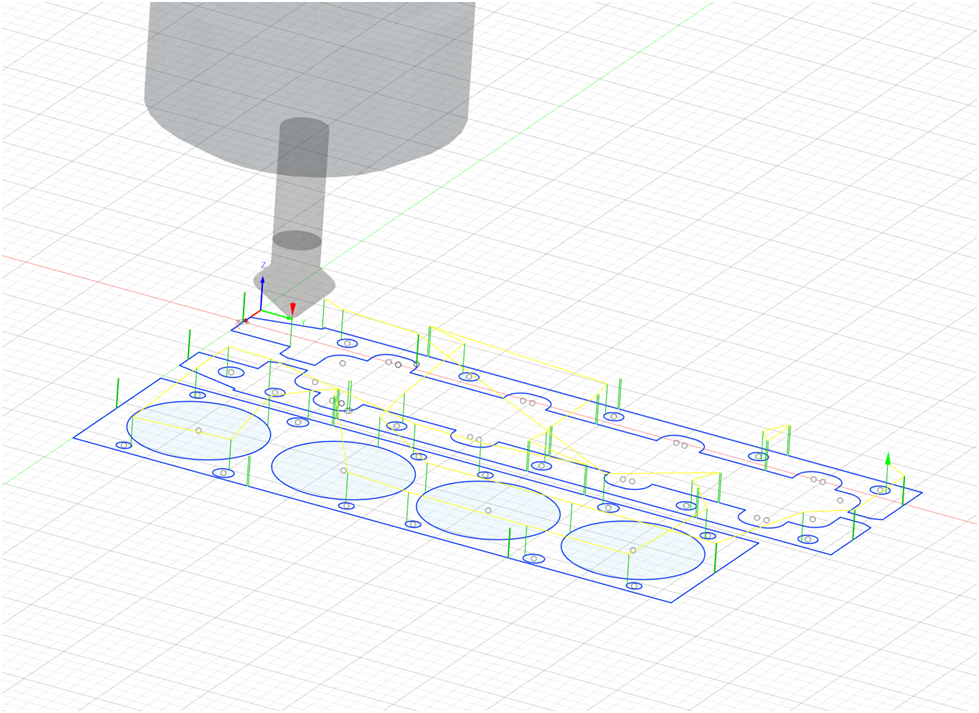
I then made a bracket for the cutter for my 3D printer.
Well, after about a week of developing and improving the adapter to allow the cutter to be mounted to the 3D printer carriage, and getting good Gcode, I began making test cuts. But like so many other things in our racket, the 3D printer carriage was not rigid enough; all of my circles came out as ovals. A 3D printer head is not designed to take much side load. Instead of continuing any further I decided to switch to the CNC router.
I made an adapter for the cutter so I could mount it in an ER25 collet in the CNC router. The Gcode from fusion 360 could be used directly on the CNC Router.
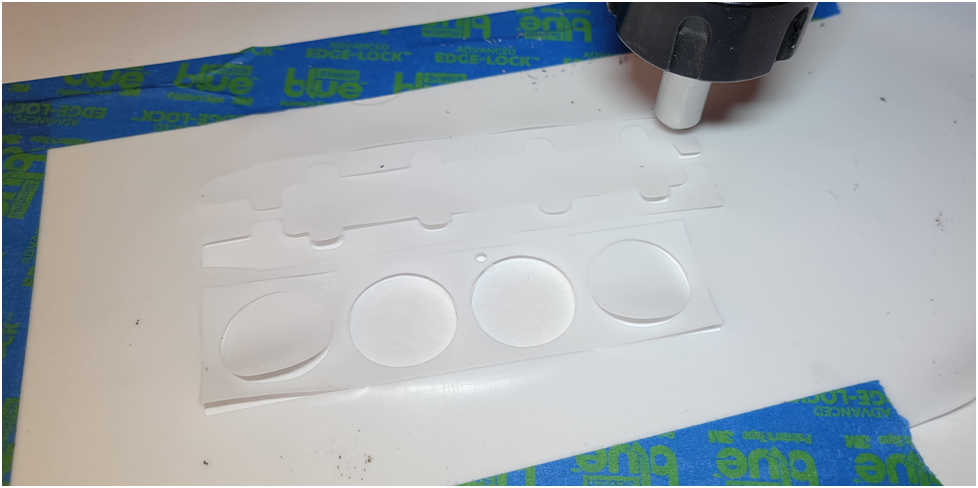
This worked much better. Below is a picture of the results of my first attempt at making gaskets on the CNC router.
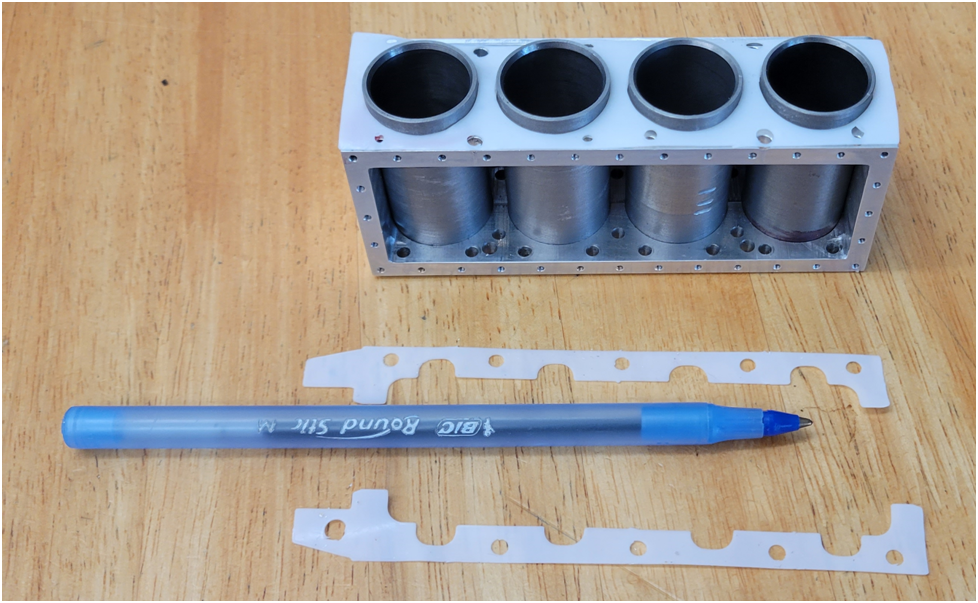
Next time I will cut all of the holes first and the outlines last. Once the outlines are cut, the gaskets can move around a little, and the holes do not come out perfectly round.
Now I need to design the rest of the Gaskets.