Offy Exhaust System
Below are a couple of photos of Offenhauser Exhaust systems. Mine will be fabricated from a brass flange plate, four 3/8″ 90 degree bent 304 stainless steel tubes and one conical collector made from a 16mm X .5mm 304 stialness steel tube.
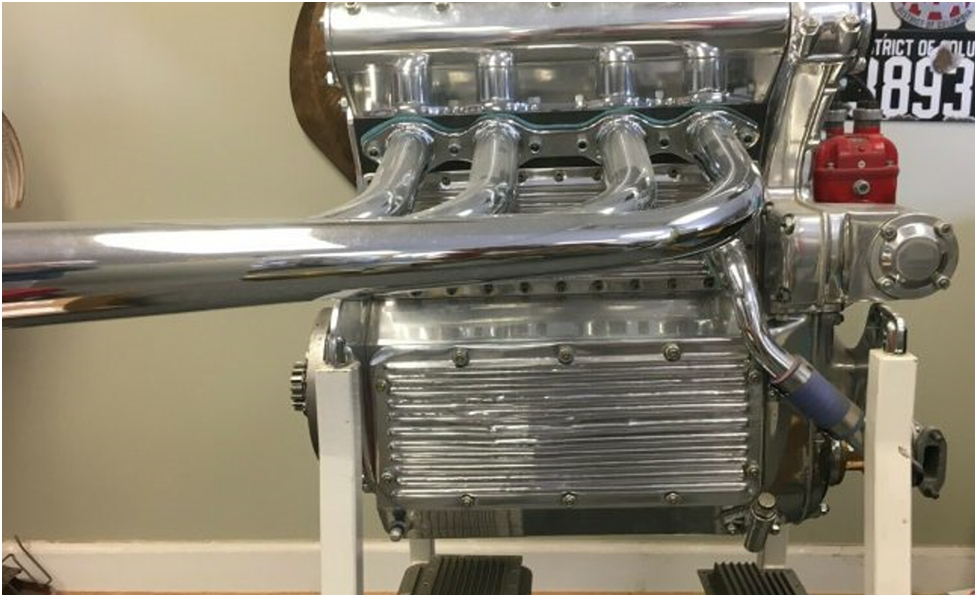
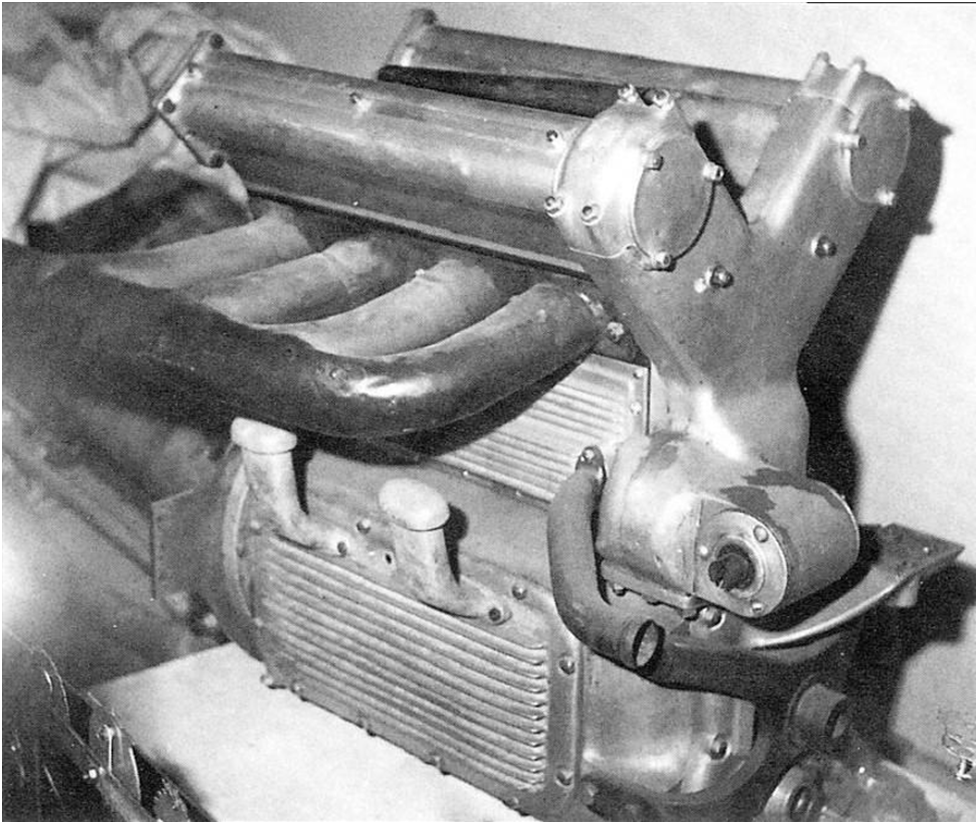
Below are a couple of views of the 3D model. Frankly I just adjusted the lengths and conical collector flare until I thought the exhaust system looked good. I reviewed Terry Mayhugh’s method for making his Offy exhaust system and will attempt to follow his lead.
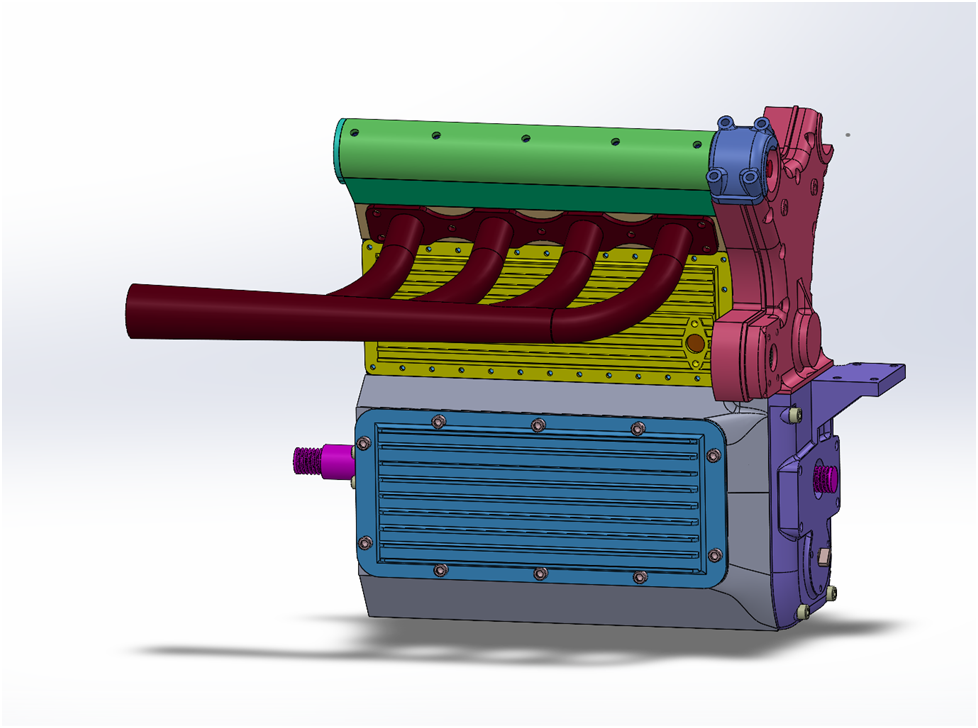
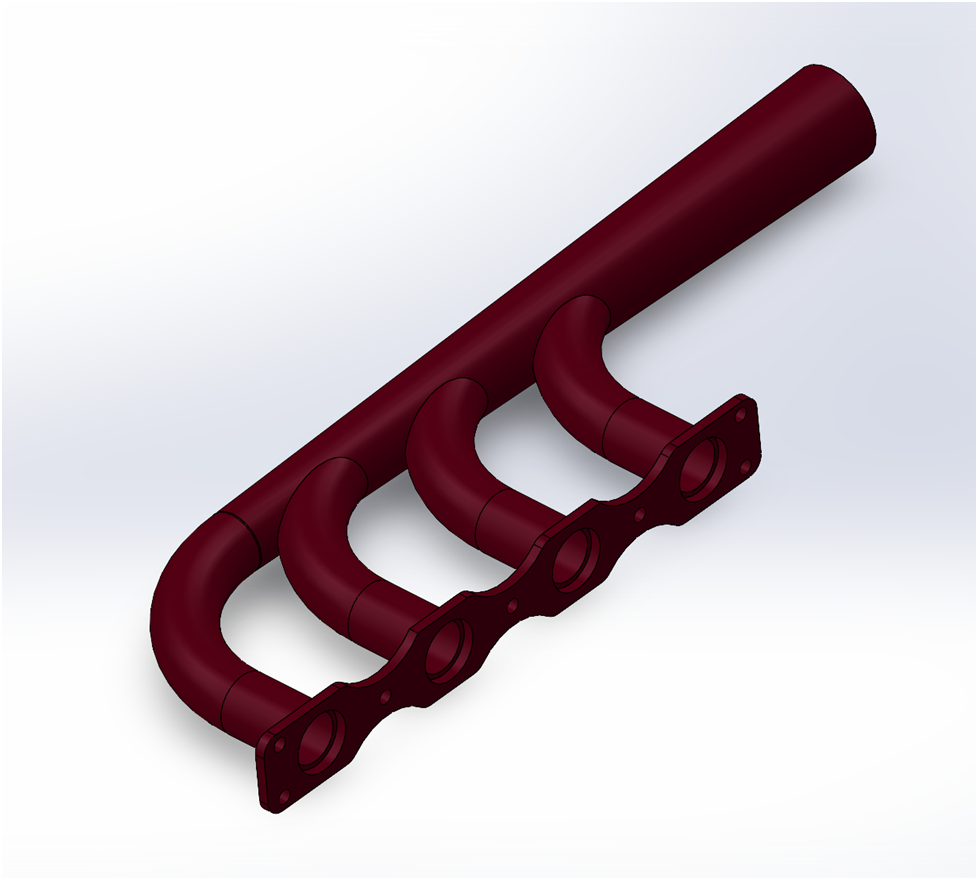
Below is the most complicated part, the conical collector. It is just under 5 inches long, 3/8″ at one end and 16mm (~5/8″) at the large end.
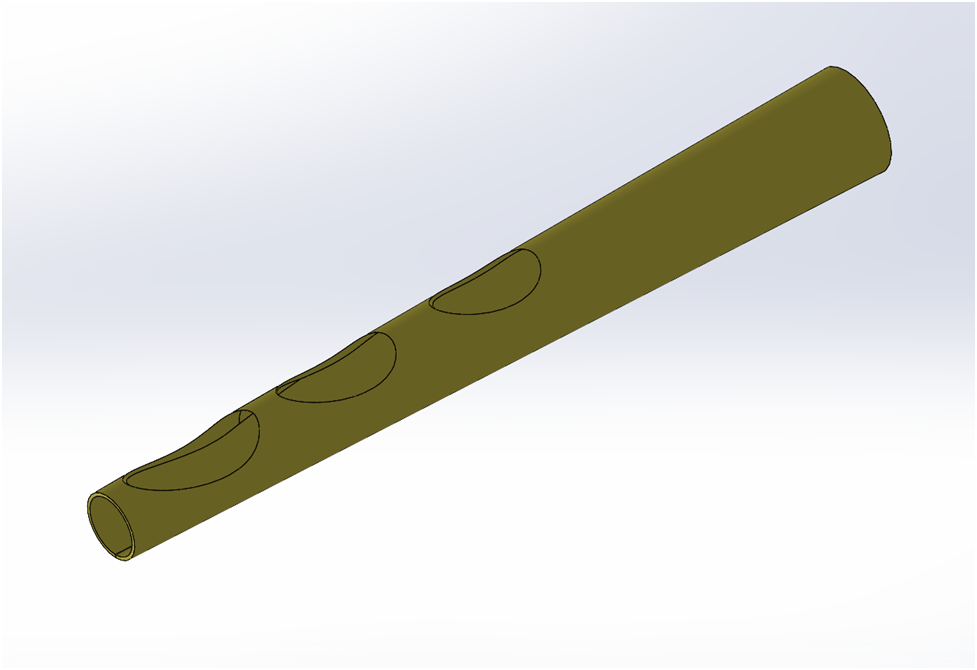
First I made a couple of fixtures. The internal mandrel started as a 5/8″ diameter length of aluminum stock, tapered to match the inside of the cone. There are two ways to machine this, the cleanest is to adjust the tail stock so it is offset to one side the difference between the two radius of each end of the cone. I chose a second method because I did not want to have to re tram the tail stock when I was done. So I used the compound to cut a taper equal to the cone reduction angle. I took cuts in 1/2″ increments down the length of the stock.
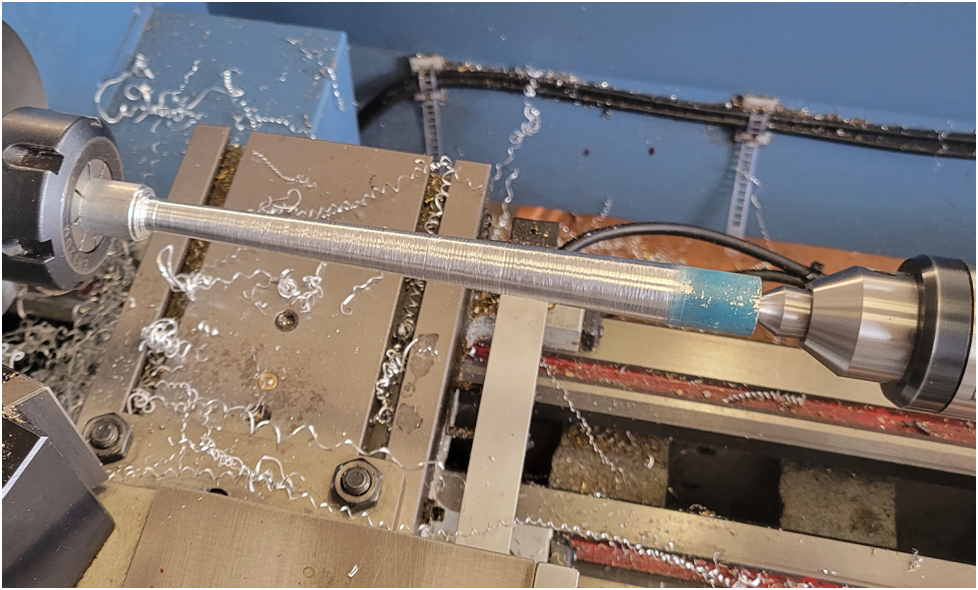
I 3D printed female molds of the cone as shown below using 9 layers around the perimeters and 60% infill. These forms are almost solid plastic.
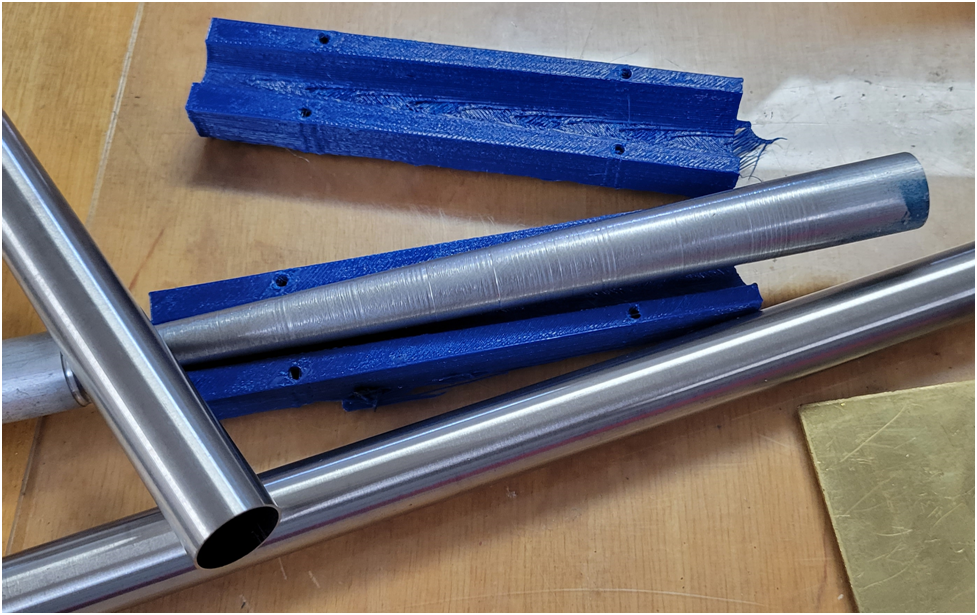
I cut a triangular notch out of a length of 16mm tube using a Dremel cut off wheel, then used the mandrel and forms to shape the cone closing up this gap. This was very tricky and the .5mm thick stainless steel was not easy to reshape. I then welded the slot closed, this was also a very tricky operation as the .5mm (~.020″) thick SS is very hard to weld without just melting it. I made a bit of a mess, but the part came out OK after grinding. I don’t know if I could do any better on a second try. I suppose I could go back and fill in some of the voids with the MIG welder, but it is so easy to just punch a hole in the tube. I will try to fill the last voids with silver solder later. I have not decided what finish I will use on the exhaust system, nickel plate or just a black high temp coating.
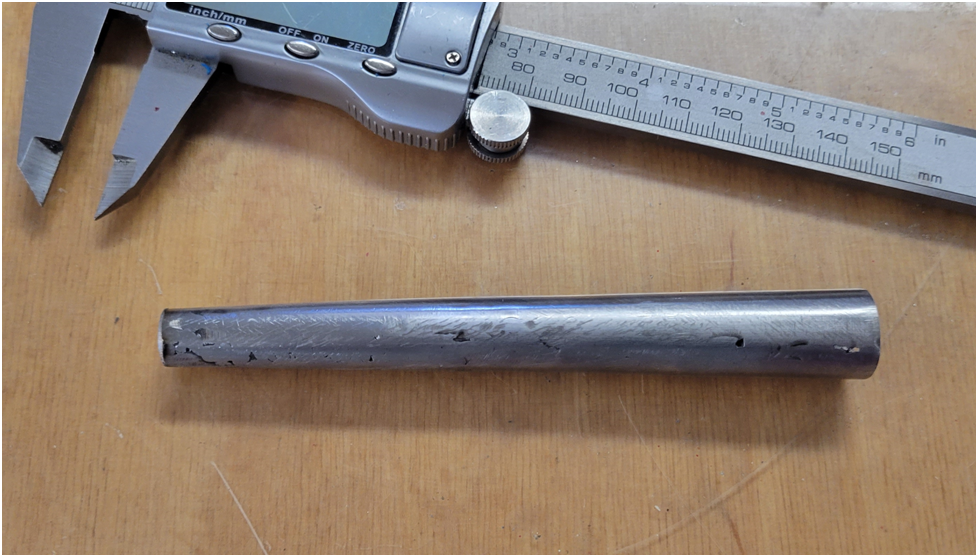
I then bent the four 3/8″ diameter SS tubes.
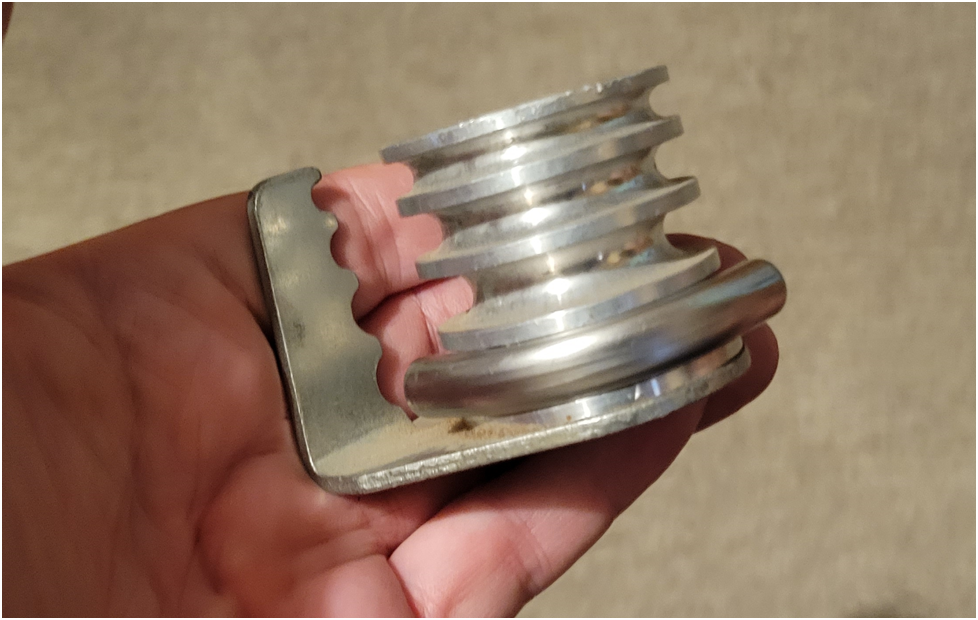
I machined the exhaust flange plate that will mate to the cylinder head out of brass sheet.
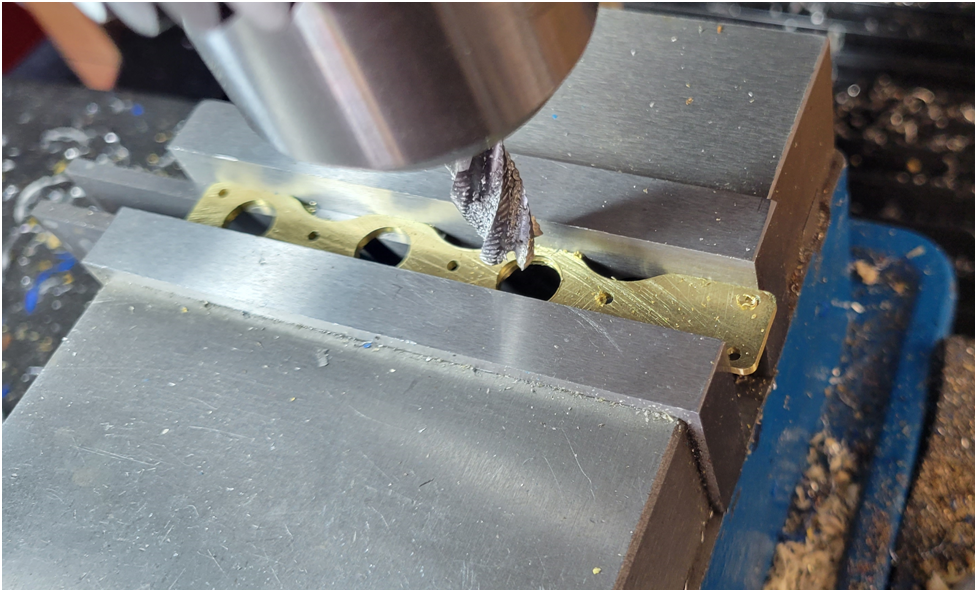
This is where I stand now. I have a little more thinking to do. I want to cut the three holes in the collector tube to match the bent feeder tubes, but am having problems with my CAD program. I thought I could punch the holes as shown in one of the earlier CAD images of the collector tube, then unroll it, or flatten it, like a piece of sheet metal, but I am not having any luck. Then I could print this out on a piece of paper, over lay it on the collector tube, and cut the holes. This still seems the best plan, I just need to figure out how to make SolidWorks cooperate.
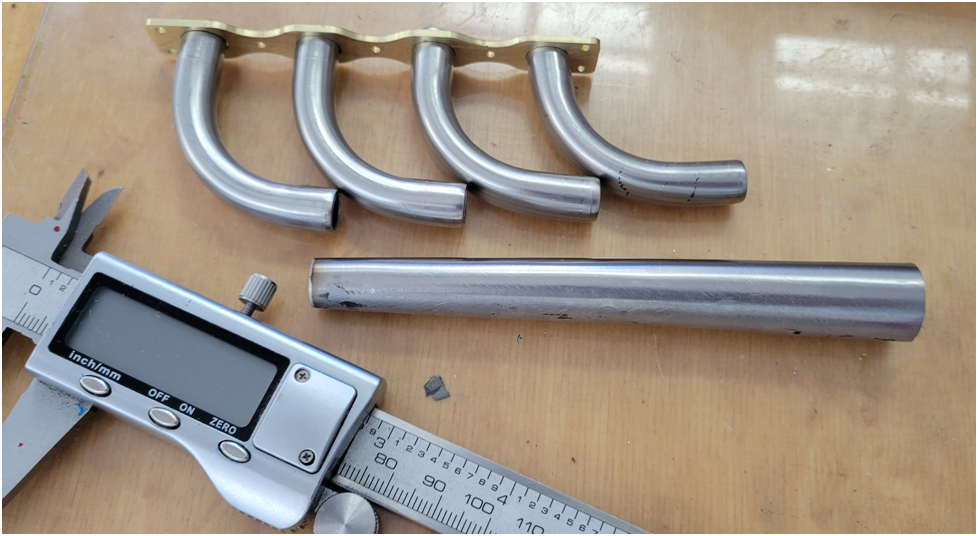
I also will make a rigid fixture to hold all the parts in the correct orientation so I can easily silver solder it all together. I need to think about this a bit as well.
All for now, I think I have completed the difficult parts.